Understanding CIGS Thin Film Photovoltaics
Thin-film photovoltaics, or solar cells, convert light into electricity through the photovoltaic effect, which generates voltage when light hits a material. The semiconductor CIGS, composed of copper, indium, gallium and selenide, now powers many thin-film solar cells. As one of the top three thin-film technologies along with amorphous silicon and cadmium telluride, CIGS demonstrates high efficiency and low manufacturing costs. With flexible applications and continued improvements, CIGS thin-film photovoltaics will become increasingly prominent in renewable solar energy.
Scientists at the National Renewable Energy Laboratory first developed CIGS thin-film photovoltaic technology in 1995. This material effectively absorbs sunlight and converts it into electrical energy, demonstrating solar conversion efficiencies reaching 20 percent in some research. Ongoing studies explore mass production methods to expand CIGS adoption. With flexible applications and high efficiency at low cost, CIGS thin-film solar cells hold great promise for meeting renewable energy needs. Continued improvements in CIGS photovoltaics will further enhance solar power generation from this robust semiconductor material.
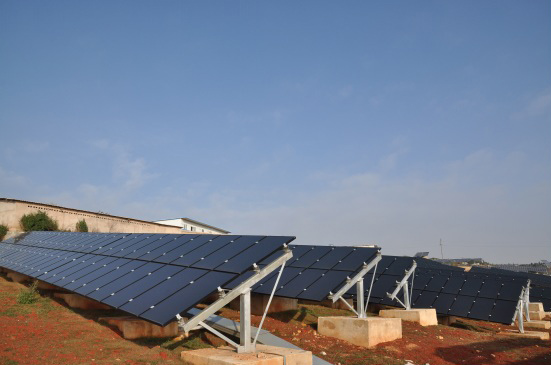
Manufacturing CIGS Thin-Film Solar Cells
Manufacturing CIGS thin-film photovoltaics starts by depositing a thin layer of copper, indium, gallium and selenide onto a substrate material. Currently, expensive production processes limit large-scale CIGS adoption, but emerging technologies aim to enable more cost-effective mass production. Potential methods include physical vapor deposition to condense CIGS onto the substrate, co-evaporation of the elemental layers, and chemical vapor deposition utilizing gas compounds. With optimized techniques, CIGS solar cell fabrication can become more economical and expand this renewable energy source.
Co Evaporation Method
A popular CIGS production method first deposits indium, gallium and selenium. Next, copper and selenium coat the substrate at higher temperature. Finally, another layer of indium, gallium and selenium is added. However, high costs and uneven elemental deposition present challenges for this co-evaporation technique. Further process refinements aim to improve uniformity and cost-effectiveness.
Sputtering Method
The sputtering technique first deposits a metal film of copper, indium and gallium at room temperature. Then it reacts the layer with selenium at high heat. This method demonstrates enhanced uniformity and smoothness compared to other CIGS production processes. It also yields higher efficiency solar cells. However, the need for elevated temperatures remains a drawback of sputtering. Further refinements aim to reduce this thermal budget while maintaining strong performance.
Chemical Vapor Deposition Method
Chemical vapor deposition enables CIGS preparation at relatively low temperatures versus other methods. However, solar cells produced through this technique demonstrate lower efficiency. Films also tend to have inferior smoothness compared to those fabricated by sputtering or evaporation approaches. Thus, chemical vapor deposition sees limited use for commercial CIGS manufacturing despite its thermal advantage. Ongoing enhancements aim to boost efficiency while retaining process simplicity.
TheAdvantages of CIGSThinFilmPhotovoltaics
l High efficiency- CIGS cells can reach over 22% efficiency in lab settings, higher than many other thin film technologies.
l Low manufacturing costs- CIGS films are deposited as thin layers, reducing material and energy usage compared to silicon cells.
l Flexible- CIGS can be deposited on flexible plastic substrates, enabling lightweight and bendable solar panels.
l Low toxicity- CIGS uses less toxic materials than cadmium telluride thin films. More environmentally friendly.
l Stability- CIGS suffers less degradation over time than other thin film technologies. Long lifetimes of 20-30 years.
l Low light performance- Works well in cloudy conditions and indirect sunlight compared to silicon.
l Light weight- With thin films on lightweight backing, CIGS provides more power per weight.
l Aesthetics- CIGS can be made semi-transparent and colored for building-integrated applications.
l Custom shapes- Can be cut, bent, rolled for specialty applications like vehicles or wearables.
Uses of CIGS Thin-Film Solar Cells
CIGS thin-film solar cells now commonly replace crystalline panels for rooftop installations. With high temperature stability and long lifetimes exceeding 20 years, CIGS performs well on roofs despite weather fluctuations. The lightweight, flexible nature of CIGS also enables mobile applications. For instance, portable CIGS solar chargers can power small electronics like flashlights and wifi hotspots on the go. Additionally, CIGS photovoltaics are ideal for off-grid street lighting. Their ability to generate electricity from low light makes CIGS well-suited for streetlamps in remote areas lacking reliable energy infrastructure. With simplicity and customizability, CIGS solar cells integrate seamlessly into street lamp designs. Whether fixed on rooftops or powering lamps in rural villages, CIGS photovoltaics deliver renewable energy access through their versatility. Ongoing enhancements will open up further possibilities for this thin-film solar technology.
Conclusion
With high versatility, efficiency, and customizability, CIGS thin-film photovoltaics hold immense potential as a solar technology. While research continues to address current limitations and improve cost-effectiveness, the future looks bright for CIGS. With ongoing enhancements, CIGS solar cells will likely gain wider adoption and make greater contributions to renewable energy.